What are the key advantages of pressure sintering compared to others reliable metallic interconnection technologies? It is demonstrated that pressure sintering surpasses all other applications for power packages.
Sintering technology is growing up fast in the last years and it will be much more present in various industrial fields. Automotive industry is one of the most ready and it is now creating a huge demand for sintered power modules.Sintering is especially suited to high-temperature applications with extraordinary requirements in terms of lifetime and reliability. The increase of temperature in power electronics applications usually causes a decrease of reliability and components lifetime. However pressure silver or copper sintering, combined with silicon carbide (SiC) devices, can easily deal with high-temperature.
Silicon carbide (SiC) is now considered the first semiconductor base material that consists in pure silicon (Si) and pure carbon (C) with enormous advantages in terms of:
- Higher operating temperature;
- Improved heat dissipation;
- Lower switching and conduction losses.
Silicon carbide belongs to the wide bandgap (WBG) family of materials. It has a very strong physical bond, giving the semiconductor a high mechanical, chemical and thermal stability. This last feature combined with the wide bandgap allow SiC to be used at junction temperatures higher than those of silicon.
Thanks to these amazing properties and advantages, SiC is today semiconductor material of choice for the use in power modules.
Several lifetime tests in comparison, with same conditions of temperature, showed how sintering is required to get the best from silicon carbide’s electrical and thermal properties when used in EV power modules. Pressure sintering definitely surpasses tin-lead soldering.
WBG materials will push the temperature bottleneck away from the device junction temperature to packaging materials. These materials will also enable smaller dies to handle larger power levels, thus increasing the areal power density. The combination of higher power density and higher frequency operation will result in smaller and more integrated power electronic packages.
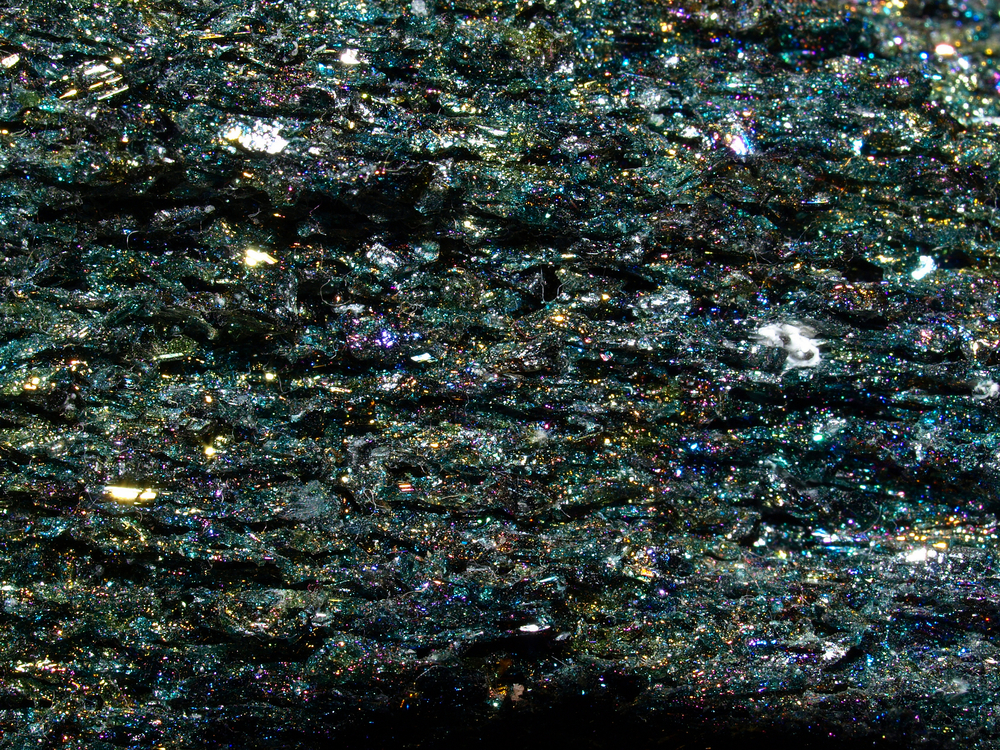
Pressure sintering advantages
What are the key advantages of pressure sintering compared to others reliable metallic interconnection technologies? It is demonstrated that pressure sintering surpasses all other applications for power packages. In a world where all the manufactures are trying to increase power density, pressure sintering shows the highest melting temperature (>400°C), the best performing electrical and thermal conductivity, best results at X-ray and at ultrasonic microscopy and much higher lifetime.Lifetime testing (Active Power Cycling +30°C / +180°C) show far more outstanding results of pressure Ag- Sintering interconnections with showed values up to 100 times compared to standard soldering.
In addition, temperature shock testing (between -55°C / +175°C) show how solder joints reach their limits around the temperature of ~150°C.
Considering electronic devices continue to shrink in size and at the same time increase in power, the trend toward higher power density is fast increasing. Volume power density is a crucial consideration where space is constrained or where maximum output is needed in a fixed space.
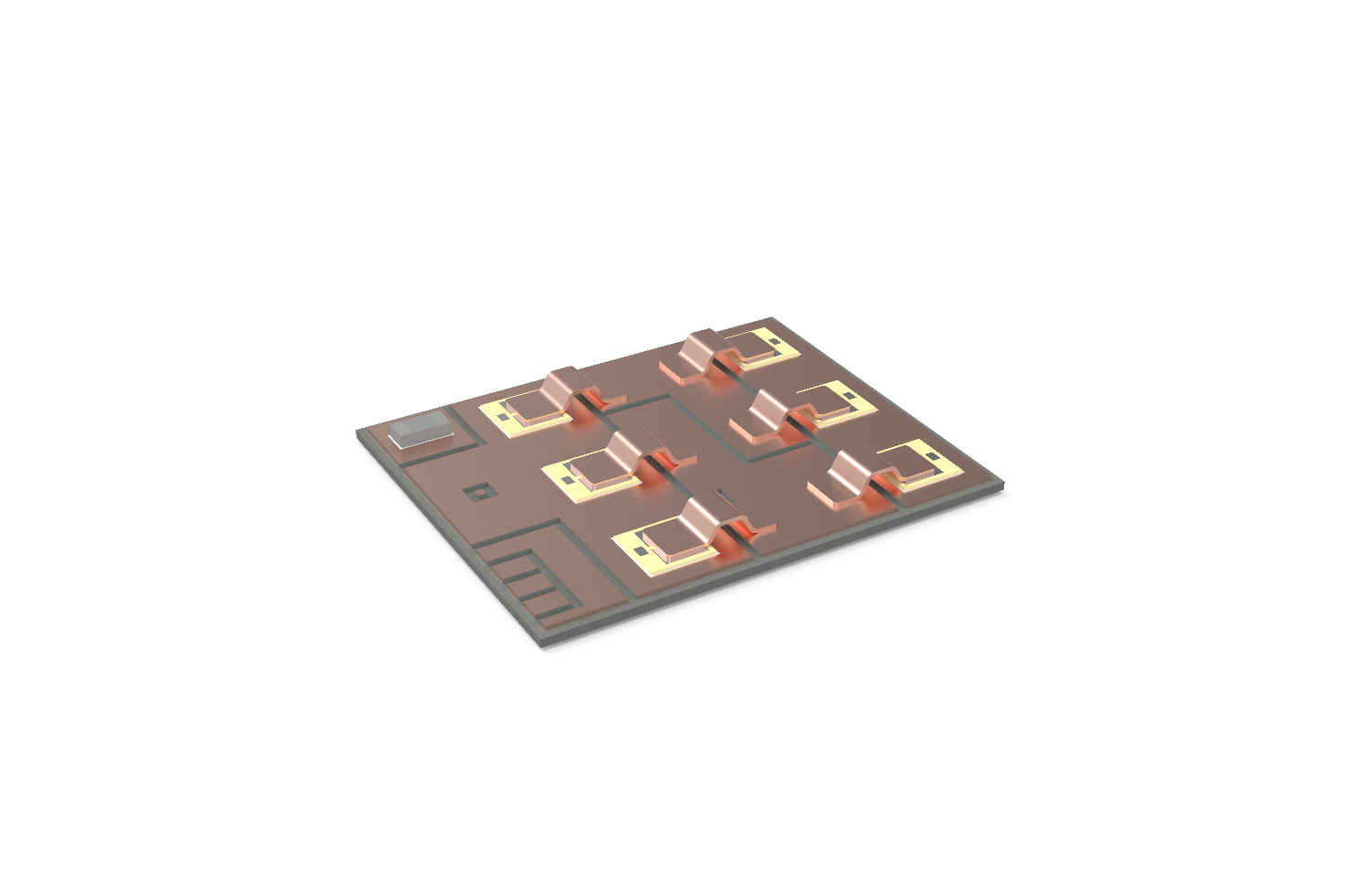
Rendering by AMX Automatrix srl
There is a constant research to reduce as much as possible the power module size with new technology generations. This new condition asks a much more precise and dedicated technology. The substrate (DBCs) of new generation will be smaller and the dies on the top very close to each other and in some case, they also need clips connections.
In these cases AMX patented Micro-Punch tool becomes the unique way to press independently every single die and clip in the most accurate way, avoiding voids and/or die cracks.
Pressure sintering is a heat treatment process applied to a powdered material in order to give it higher strength, integrity and conductivity. Sintering is now considered the most reliable technology for power electronics packaging.
As a matter of facts, only through sintering is possible to reach:
- Highest melting temperature >400°C
- Best thermal conductivity coefficient >150 W/(m K)
- Best electrical conductivity coefficient and lower electrical resistivity
- Best result on lifetime testing
Pressure sintering can definitely fit better with all the power electronics layouts, usually called “advanced package”:
- High-integrated modules (i.g clips attach, embedded dies);
- Different levels (i.g. double side cooling packages);
- Different material, surfaces and process.
Sintering materials
In the last years, mostly due to innovations in nano-particle materials, greater emphasis on energy and eco-sustainability, the die attach leadfree techniques have attracted considerable interest.Silver sintering is now the one of the frontrunner non-lead containing die attach solution.
Sinter paste is made of monometallic particles and a resin is printed onto a substrate in patterns corresponding to the shapes and locations of the silicon carbide dies. The substrate is heated up to evaporate the volatile content and the dies can then be placed.
The sintering process is a combination of high temperature and pressure (a downwards force on the top of the dies).
The high pressure - starting from a few MPa up to ~40 MPa - offers several advantages:
1. Much more efficiency in the bonding process at a lower process temperature;
2. The bonds achieved will be able to operate and resist during its lifespan in a most thermal stressed environment;
3. It greatly reduces the risks of voids; even a small void percentage can lead to delaminating and cracking dies over time.
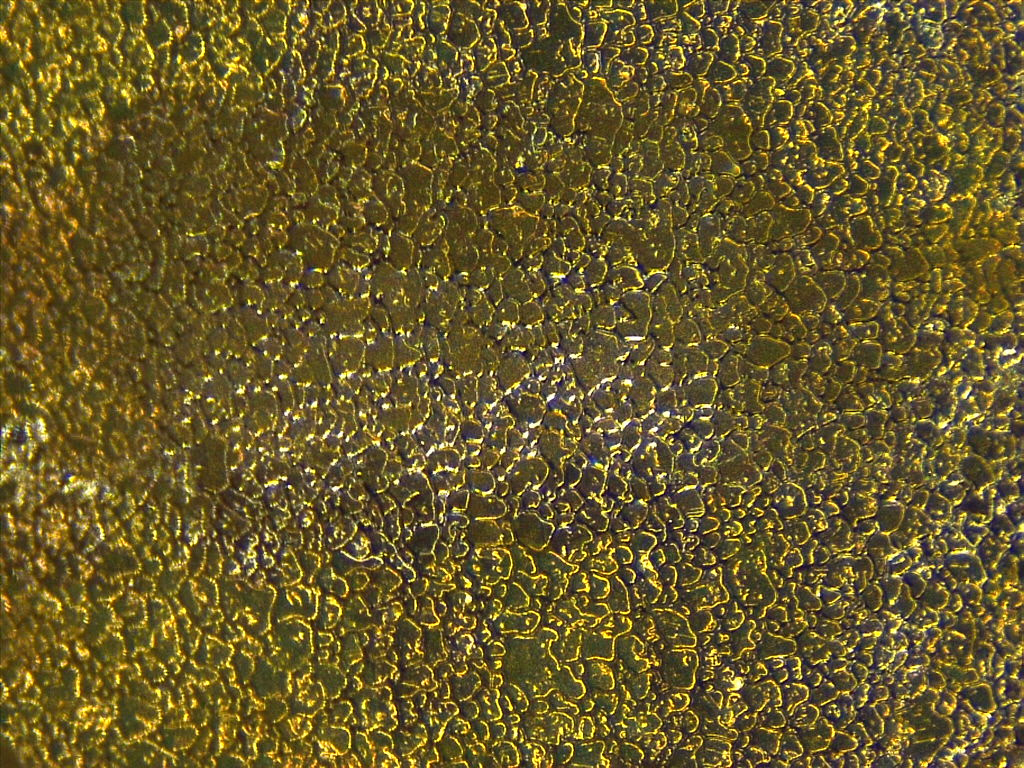
Silver (Ag) is currently the most popular sintering material.
Melting point is approximately around 960°C and the thermal conductivity of a silver sinter paste is between 130 and 250W/ m K.
Silver sintered paste retains the benefit of epoxy attach, it holds the components in place for handling and so increases the total throughput of the process.